超薄类挠性板单面真空热压半固化片填孔工艺研究
发布日期:2023-08-03
1 背景描述
受限于刚性PCB(硬板)工艺技术对板厚的限制,类似挠性板(类软板)的市场需求促使对于硬板替代技术的研究提上日程。为改进超薄类软板PCB产品的塞孔品质及产出效率问题,我公司研发在满足品质要求的前提下,进行一种成品板厚≤0.15 mm的双面类软板产品的树脂塞孔工艺替代传统塞孔工艺的技术研究。
2 现有树脂塞孔工艺在超薄类软板PCB产品生产方面存在的问题分析
业界传统的树脂塞孔工艺是网版印刷塞孔(丝网或铝片网版),采用刮刀压力将树脂油墨塞入导通孔(via)内。常规可生产树脂塞孔纵横比≤7:1,最小孔径≥0.15 mm,最小板厚≥0.3 mm。传统工艺可满足常规via孔树脂塞孔要求。树塞纵横比>7:1业界常规采用真空塞孔机生产。
双面板树脂塞孔非盖孔树塞工艺微观流程:电镀→压板翘(避免板翘问题导致塞孔及研磨不均)→树塞治工具(丝印网版、导气底板)准备→树脂油墨解冻回温→塞孔印刷→预烘烤→研磨→二次烘烤固化(部分树脂油墨为便于研磨,将一次固化参数降低,研磨后需要二次高温烘烤固化)→干膜。
传统树塞工艺对≤0.15 mm超薄板生产工艺存在的问题:(1)塞孔插框热风烘烤散框;(2)塞孔树脂凸出(墨凸)、丝网印刷反粘凹陷、via孔塞孔透光;(3)树脂研磨不净、研磨过度露基材;(4)研磨不均且研磨次数过多>3次,切屑研磨导致基板涨缩变异。
3 可行性实验方案拟定
(1)由丝印网版塞孔,改为压机真空单面热压半固化片(PP)树脂填胶塞孔。
(2)方案微观流程为:电镀→棕化→PP裁切+冲铆钉孔→离型膜钻孔→铆合作业→真空压合→拆解→研磨→干膜。
(3)各微观工序加工说明。
①棕化:待塞孔板件过棕化处理,目的是提高树脂与孔壁结合力。
②塞孔填胶PP加工:裁切尺寸同板子等大+将填胶PP的4个角钻孔处理。
③离型膜钻孔:量测实际板子涨缩,申请同比例涨缩程式对离型膜进行钻孔。
④铆合作业:将钻孔后的离型膜(可耐250 ℃高温)+PP+待塞孔板件铆合。
⑤真空压合:选用类软板真空压合塞孔专用配方压程,依叠构将铆合好的板子叠入压机,上下与钢板接触面铺完整无孔离型膜,离型膜尺寸比板子大20 mm单边。
⑥拆解:将组合层离型膜去除,裁切短边8 mm,去除掉铆钉孔,即可轻松分离同组铆合板件,同时将中间PP撕除即可。
(4)叠构设计如图1所示。
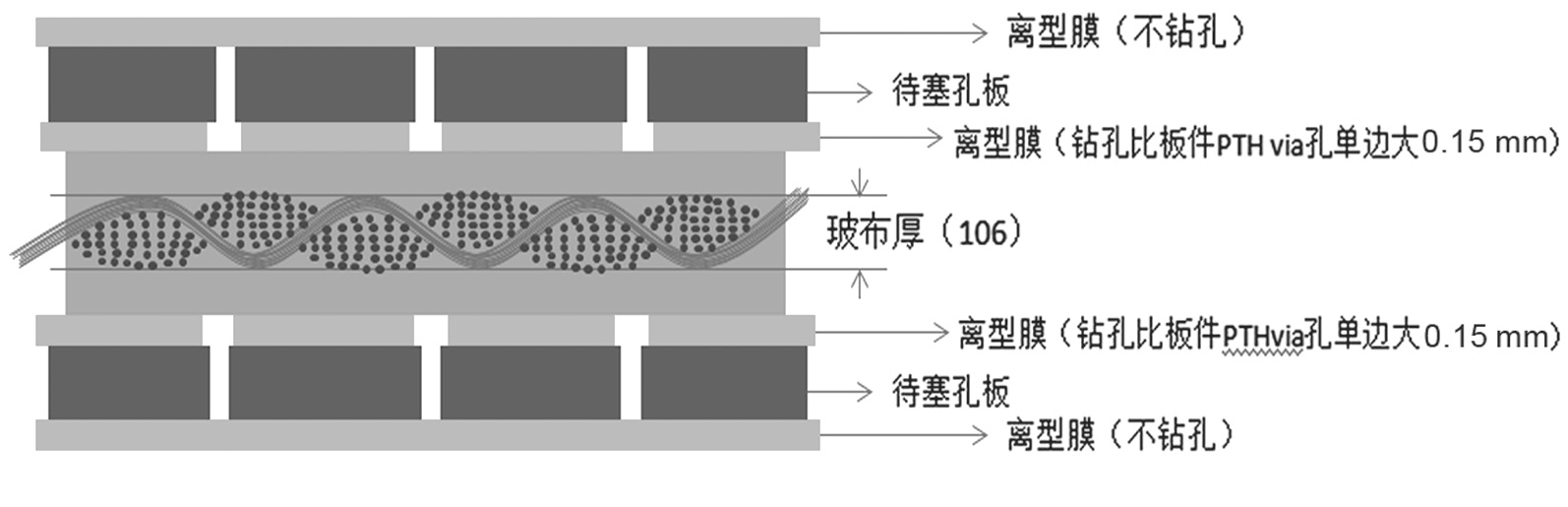
图1 单面热压PP填孔叠构设计示意图
(5)压机程式选用如图2所示。
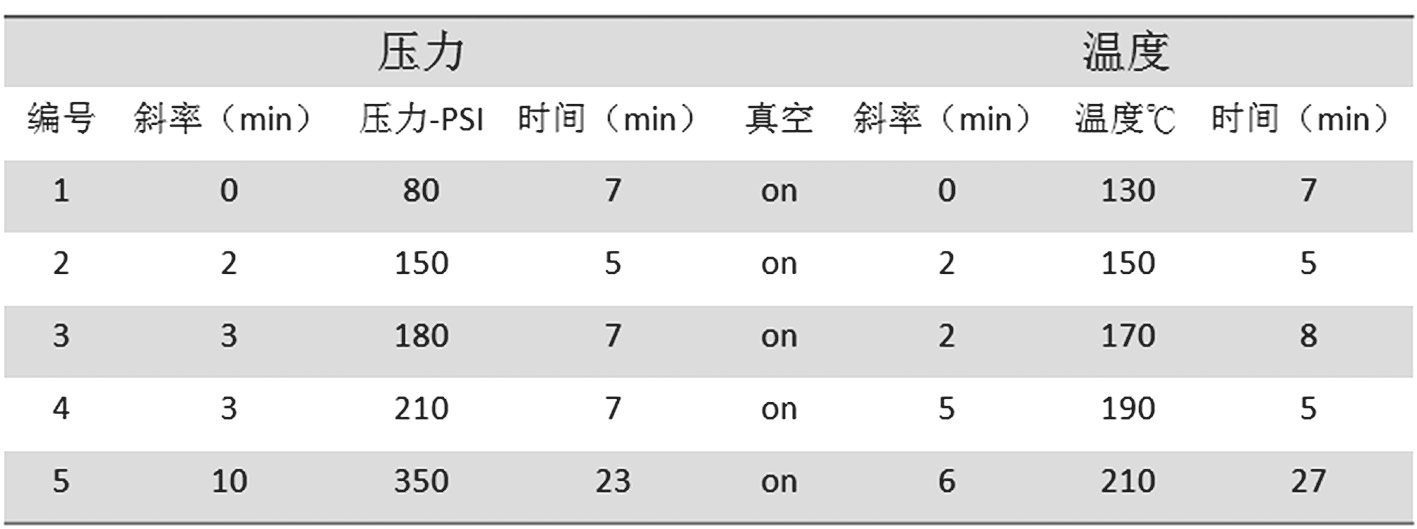
图2 真空压合塞孔专用压程表图
(6)铆钉裁边如图3所示。
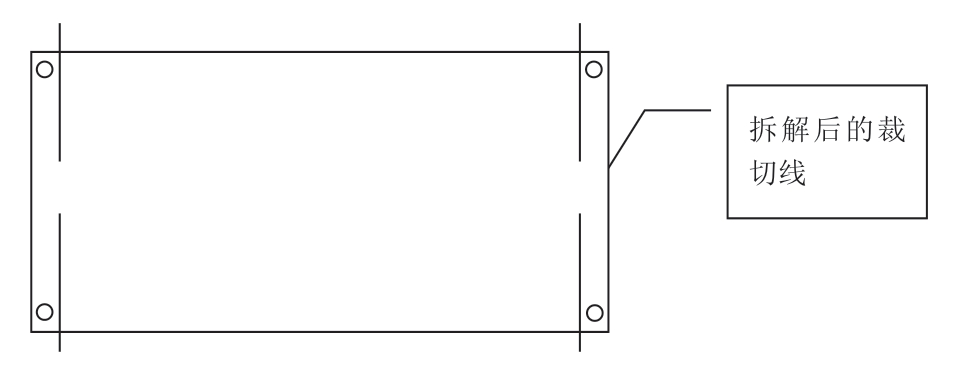
图3 拆解作业铆钉裁边
4 方案实施过程与结果
依据实验方案导入实施验证,并追踪试产批,对塞孔、研磨、研磨后涨缩、新旧工艺产出效率、综合成本效益等项目做全流程跟踪评估。
(1)压合:将板子、离型膜、PP依叠构顺序完成铆合,大张叠板6 pnl/层,叠12层/open,8 open/锅,厚度不足以钢板填充。上下15张全新牛皮纸,最外层离型膜需>板子尺寸10 mm单边。避免树脂溢出反粘污染钢板。
(2)压合后塞孔品质确认:塞孔处溢胶扩散范围约0.3 mm左右(如图4所示),溢胶区间较大,验证批仍有调整空间(实际应用可根据实际填孔溢胶情况适当调整PPRC树脂含量)。
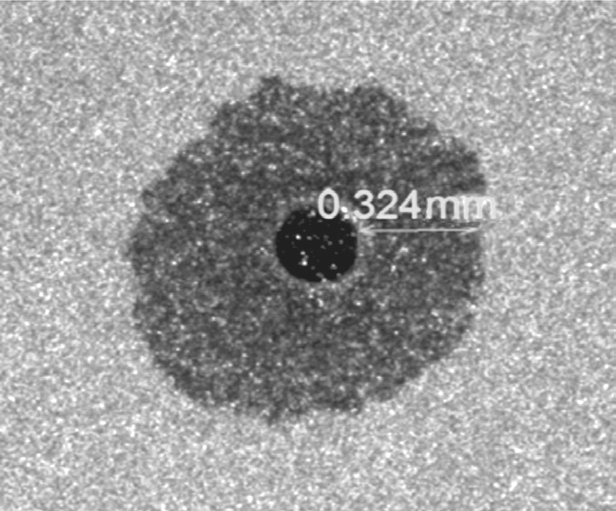
图4 压合溢胶
(3)压合后塞孔微切片分析:树脂填塞溢胶面平整,且外溢厚度与铜面平齐无凹陷,溢胶面切片(离型膜有良好的阻胶溢胶效果)。树脂填胶面拆解剥离后的PP有凸起残留,实际凸起厚度仅0.06 mm左右远低于树脂塞孔墨凸0.12~0.15 mm(如图5所示)。
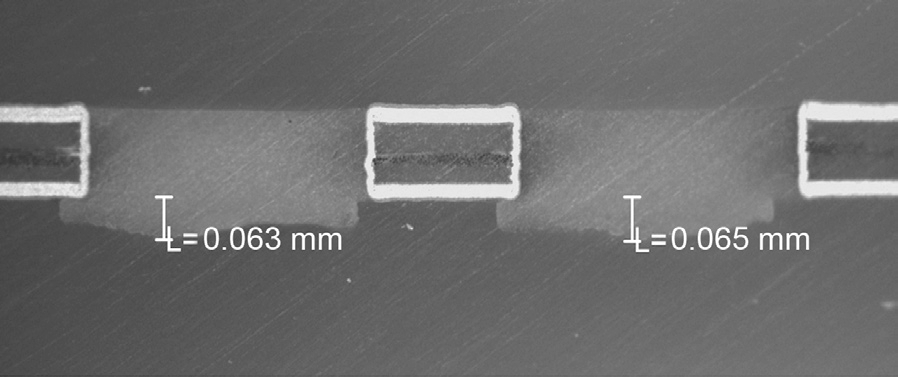
图5 压合溢胶切片
(4)研磨:塞孔后正常工艺研磨,溢胶面及塞孔面孔口树脂研磨1次即可研磨干净(如图6所示)。研磨1次与研磨3次涨缩变化数据对比,一次研磨后板材涨缩量小且稳定。
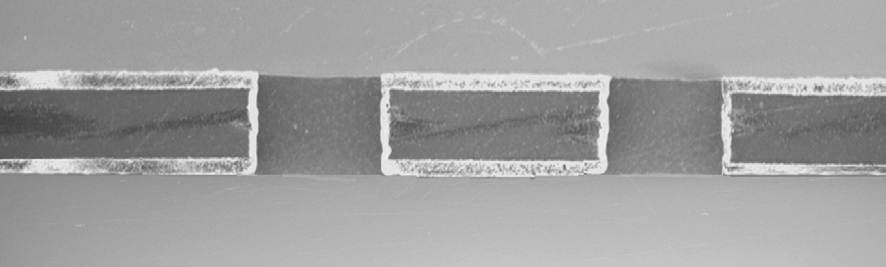
图6 树脂研磨干净
(5)单面热压真空PP填孔工艺产出效益与传统树脂塞孔对比分析见表1所示。
表1 热压PP与树脂塞孔对比表
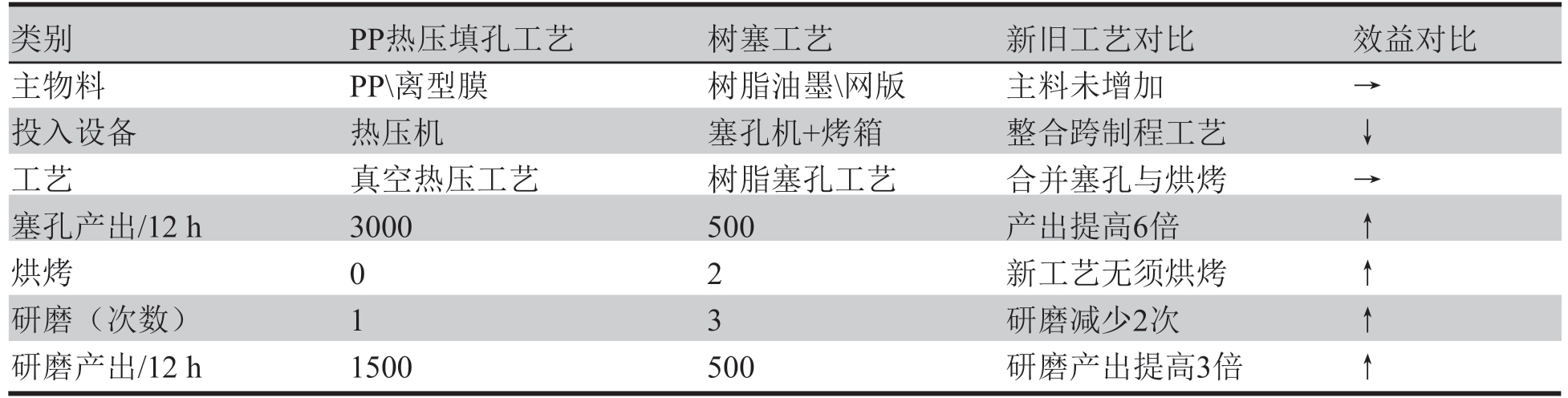
PP热压填孔工艺投入物料(PP、离型膜)较树塞工艺投入(树脂油墨、丝印网版)成本接近等同。PP热压填孔产出较树脂塞孔增加6倍,研磨次数减少2次 ,研磨产出增加3倍。综合效益对比:PP热压填孔工艺>树脂塞孔工艺。
5 工艺关键控制项目
(1)塞孔填胶PP裁切尺寸同板子等大,同时将填胶PP的4个角钻铆合孔,钻孔孔径比铆钉孔大0.1 mm单边。PP选用106-RC60%以上,可依照塞孔板件孔数计算需求填胶厚度,再根据PP塞孔填胶量计算精确选择所需PP的RC含量。PP的Tg选择依照客户需求为准。亦可用较大流胶量的纯胶生产,但是成本较高。
(2)离型膜钻孔:量测实际板子涨缩,申请同比例涨缩程式对离型膜进行钻孔。板件塞孔点离型膜钻孔比板件PTH孔单边大0.15 mm,离型膜铆钉孔与板件相同。离型膜为无硅高分子哑光离型膜,离型膜厚30~36 μm均可,易撕除,无残胶,扩散小。
(3)铆合与压合:将钻孔后的离型膜(可耐250 ℃高温)+PP+待塞孔板件完成铆合作业。选用类软板真空压合塞孔专用配方压程,依叠构将铆合好的板子叠入压机,上下与钢板接触面铺完整无孔离型膜,离型膜尺寸比板子大20 mm单边。
6 总结
对超薄类软板(板厚≤0.15 mm)有树脂塞孔要求工艺的产品,传统的树脂塞孔工艺因受塞孔墨凸影响,衍生研磨露基材、研磨不净、研磨次数过多进而衍生产品尺寸变异过大等问题。超薄类软板单面真空热压PP填孔工艺可有效解决传统树脂塞孔对超薄板PCB所存在不可避免的衍生性问题(塞孔墨凸、凹陷、研磨不净、露铜等)。且整合了塞孔前压板翘、树脂塞孔烘烤、二次烘烤固化等工艺流程,降低了研磨次数及因研磨导致的机械应力涨缩过大的问题。此工艺成本低,产出效率高且品质稳定。可满足类软板超薄产品的树塞品质要求,压合工艺成熟,在超薄类软板塞孔加工工艺方面,可替代传统树脂塞孔工艺。